共计 989 个字符,预计需要花费 3 分钟才能阅读完成。
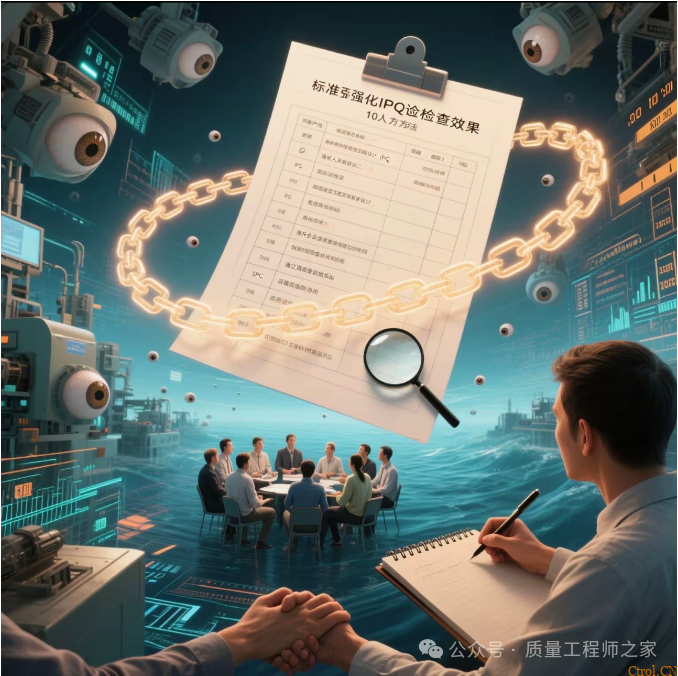
1. 制定标准化巡检表:依据产品特性和工艺要求,设计详细的巡检表,明确检查项目、标准和方法,确保巡检工作的一致性和全面性。
2. 高频次抽检:增加巡检频次,尤其是对关键工序和质量不稳定的环节,及时捕捉质量波动。
3. 动态监控设备参数:利用智能传感器和监控系统,实时跟踪设备运行参数,如温度、压力、转速等,提前预警设备故障引发的质量问题。
4. 强化人员培训:定期对操作人员和IPQC人员进行技能培训,提升全员质量意识和操作水平,减少人为失误导致的质量缺陷。
5. 建立质量追溯体系:为每一个生产环节赋予唯一标识,一旦出现质量问题,能够快速追溯到原材料批次、生产设备、操作人员等信息,精准定位问题根源。
6. 推行首件检验制度:每个班次、每批产品开始生产时,对首件产品进行严格检验,确认符合质量标准后,方可批量生产,避免批量性质量事故。
7. 运用统计过程控制(SPC):通过收集和分析生产过程中的质量数据,绘制控制图,监控过程稳定性,及时发现异常趋势并采取纠正措施。
8. 开展质量小组活动:组织一线员工成立质量改进小组,鼓励员工提出质量改进建议,集思广益解决生产过程中的质量难题。
9. 加强供应商协同:与原材料供应商建立紧密合作关系,对供应商的生产过程进行质量监督,确保原材料质量稳定。
10. 定期总结与优化:定期对IPQC巡检工作进行总结分析,评估质量管控效果,根据实际情况优化巡检流程和方法,持续提升质量管控水平。