共计 4144 个字符,预计需要花费 11 分钟才能阅读完成。
它的核心很简单:把影响产品质量的因素,归纳为六个方面——人、机、料、法、环、测。
无论是生产过程中的波动,还是成品检验中的不良,几乎所有质量问题,都可以从这六个要素中找到原因。
这六个字,不只是经验总结,更是质量管理体系中的科学分析框架,被广泛应用于质量改进、工艺优化、风险预防等场景,很多国际标准、行业规范中都明确推荐使用。
想把质量问题管好,第一步就是学会用好这六个字。
今天我们就一起拆解5M1E分析法,看它如何在实际工作中发挥作用。
https://s.fanruan.com/uyd5j
说到质量管理,很多人都会遇到一个疑惑:
明明是同样的人、同样的设备、同样的材料,为什么做出来的产品,质量总有点差别?
这个现象,在质量管理里有个专门的名字,叫做质量波动。
意思是:即使在同样的条件下生产,产品的质量特性值(比如尺寸、重量、性能指标)也会有细小的变化。
有时候,波动小一些,产品还能达标;但一旦波动过大,不良品、投诉、返工,马上就来了。
那问题来了—— 到底是什么导致了这些质量波动?
其实原因很简单,六个字:人、机、料、法、环、测。
假设你在一家餐厅吃饭:
- 人:厨师的手艺不稳定,今天盐多放了一勺,菜一下就咸了;
- 机:厨房里的炉灶火力不稳,有的菜炒得太老,有的还夹生;
- 料:今天用的蔬菜批次不一样,新鲜度差了一些,口感自然打折;
- 法:炒菜的顺序、火候控制不统一,有人快炒有人慢炒,味道肯定不一样;
- 环:天气太潮湿,厨房湿度太高,油烟机排风不畅,影响食材质量;
- 测:没有严格尝味、试菜的标准,做完就直接端给客人,问题很难及时发现
这六个环节,任何一个掉链子,菜品的质量都会变差。 如果几个问题叠加,口味波动一下就放大,最后客人投诉、退单、差评,问题全来了。
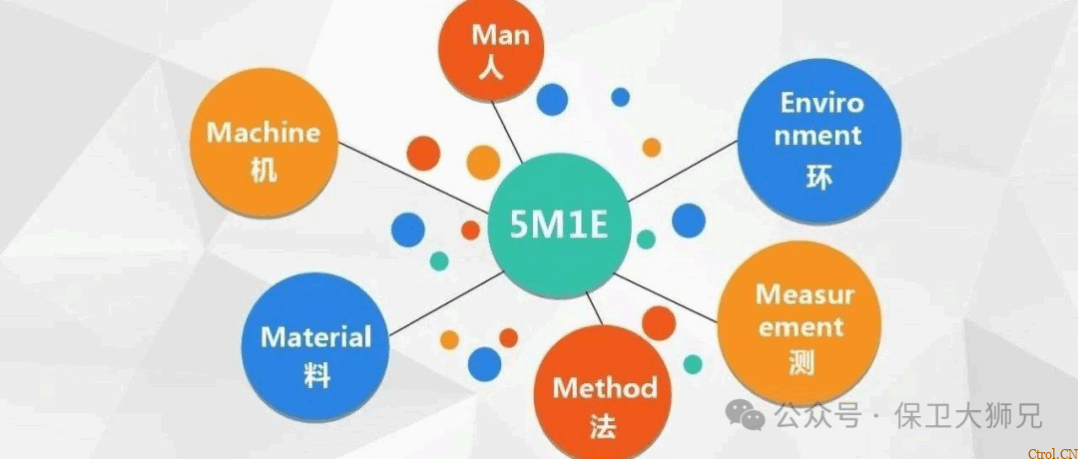
下面我就按人、机、料、法、环、测的顺序,拆解每个环节该怎么管,全部是实操落地的方法,帮你把质量抓到位。
① 人(Man)|人的问题,核心在规范、培训和责任落实
常见风险:
- 新员工操作不熟练,动作走样;
- 老员工凭经验“自创工艺”,不按规范来;
- 责任不清,出了问题互相推诿。
基础做法:
- 建立培训机制,确保每个人都受过岗前培训;
- 作业指导书必须上墙、上手,操作步骤全员统一;
- 明确岗位职责,操作员、检验员、主管各自管什么,不能含糊。
进阶做法:
- 把人员、岗位、工序、培训记录等信息集中管理,做到“谁做的、谁培训、谁负责”一清二楚;
- 把操作过程中的异常、违规、整改记录全部电子化,随时可查、可追溯;
- 定期做质量技能评比和责任考核,推动员工持续改进。
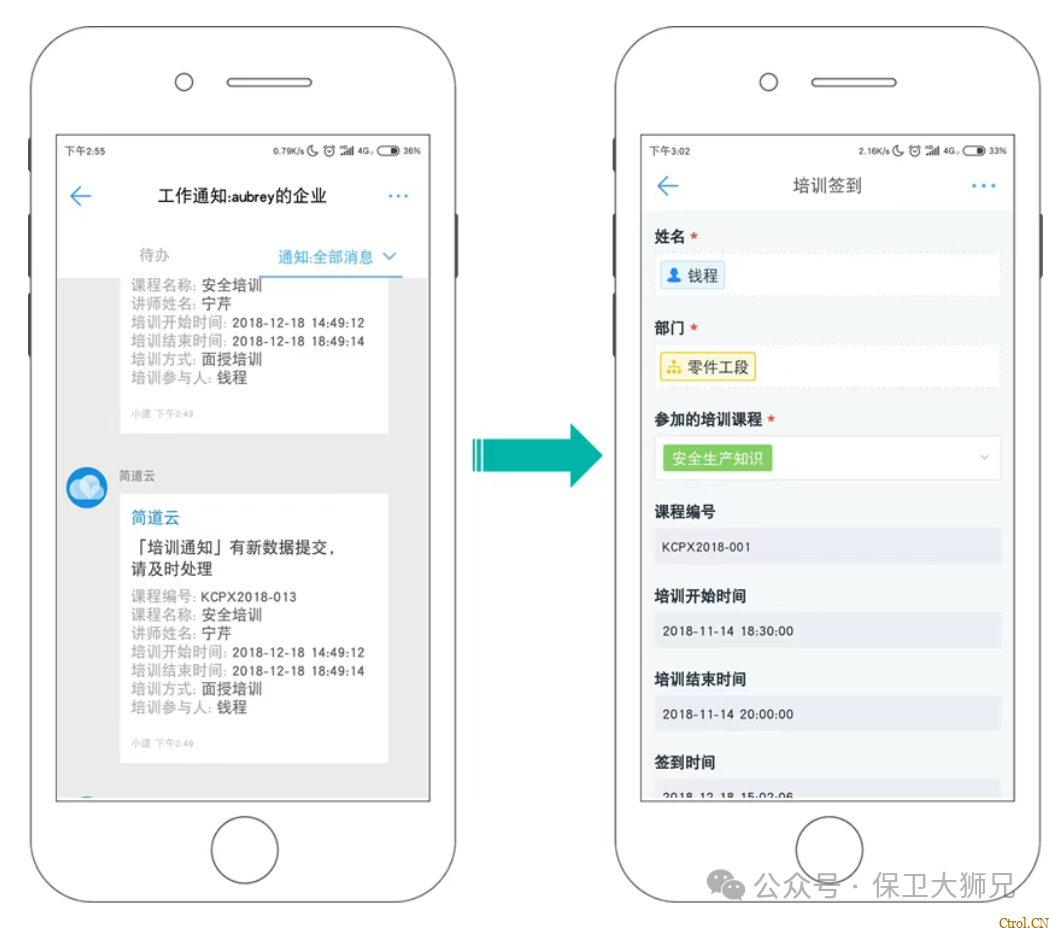
常见风险:
- 设备长期带病运行,故障率高;
- 工装夹具磨损严重,影响加工精度;
- 设备保养不到位,关键精度漂移。
基础做法:
- 制定设备日常点检、周期保养、首件检验制度;
- 建立设备台账,记录所有维修、调试、故障详情;
- 设备异常必须立刻停机检查,绝不带病作业。
建议做法:
- 把设备的运维记录、工序关联、故障预警全部打通,关键设备的状态、检验结果、异常记录能自动关联;
- 对设备运行趋势、保养周期、故障频率做数据分析,提前预防;
- 设备问题一出现,能快速关联相关工序、产品、操作人员。
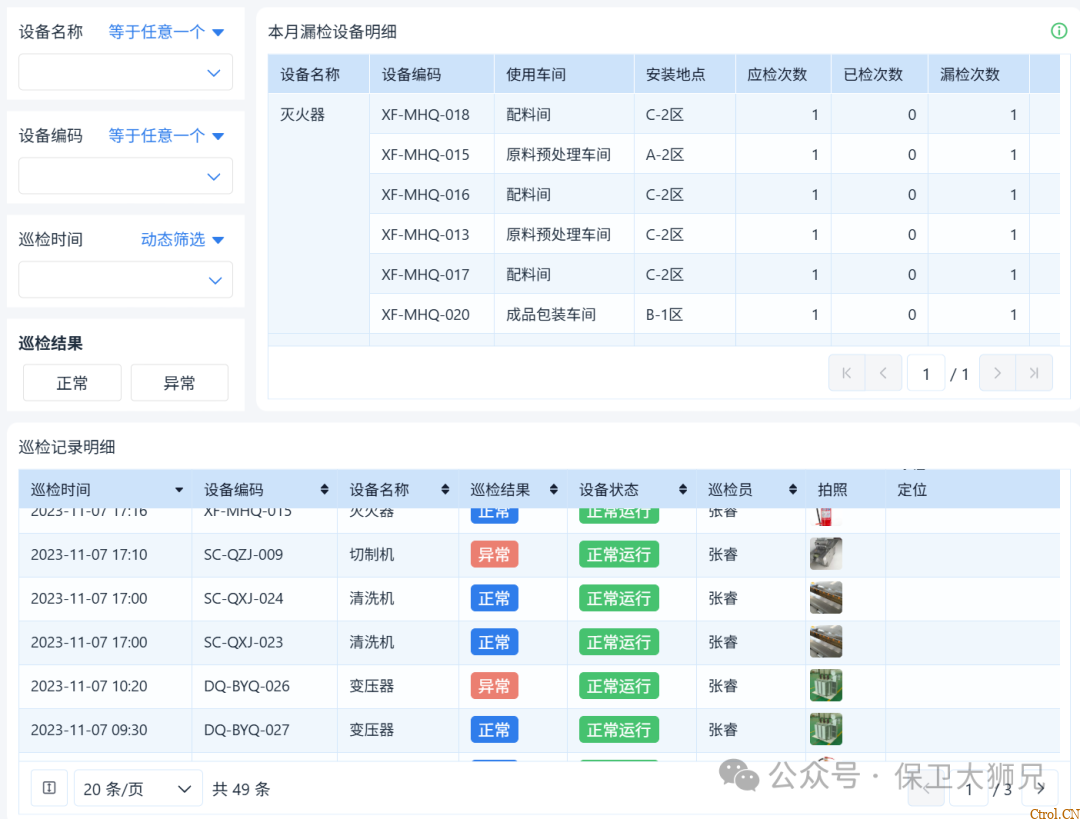
常见风险:
- 采购不严,原材料批次性能波动大;
- 来料检验走过场,不良品流入生产;
- 物料批次混用,后续问题无法追溯。
基础做法:
- 制定严格的来料检验标准,绝不漏检;
- 做好材料批次管理,每批料的流转全程记录;
- 建立供应商评价机制,按质量表现动态调整采购策略。
建议做法:
- 把物料、供应商、来料检验、批次流转信息全部打通,任何材料问题一查就能找到源头;
- 所有批次数据自动关联后续工序、产品、客户,问题可追溯、可复盘;
- 来料不良、供应商异常、物料报废等情况,都能自动生成报告、推动整改。
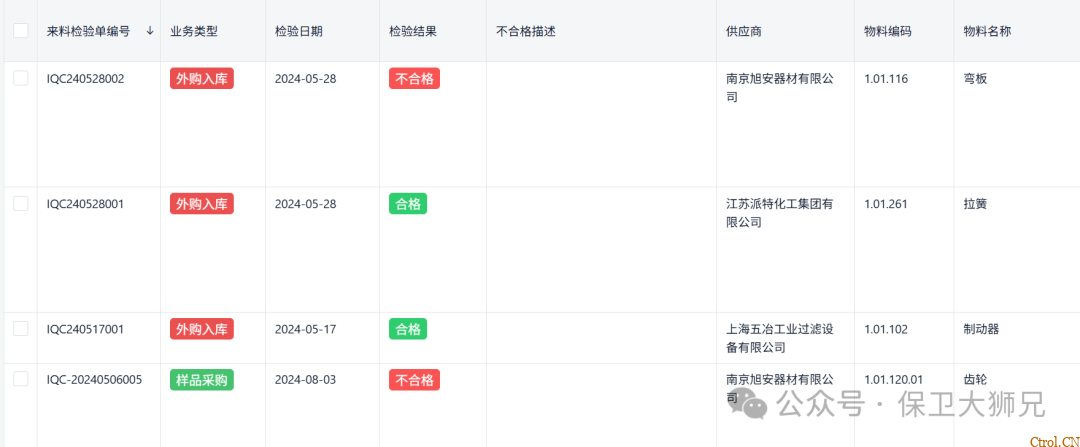
常见风险:
- 工艺流程随意改,没人管;
- 作业指导书形同虚设,实际操作全靠“习惯”;
- 工艺参数过于宽泛,不同人操作结果天差地别。
基础做法:
- 建立标准工艺流程,操作、检验、异常处理流程必须固化;
- 作业指导书必须覆盖所有关键工序,图文并茂、易懂易用;
- 工艺变更必须走审批流程,试产、验证、确认全流程执行。
建议做法:
- 把工艺流程、作业指导书、工艺变更记录集中管理,每个工序对应的工艺标准一目了然;
- 工艺执行过程中的检验数据、异常情况、操作履历全部电子化,便于追溯和对比;
- 工艺参数、检验标准、异常处理动作联动,防止“纸上标准、现场失控”。
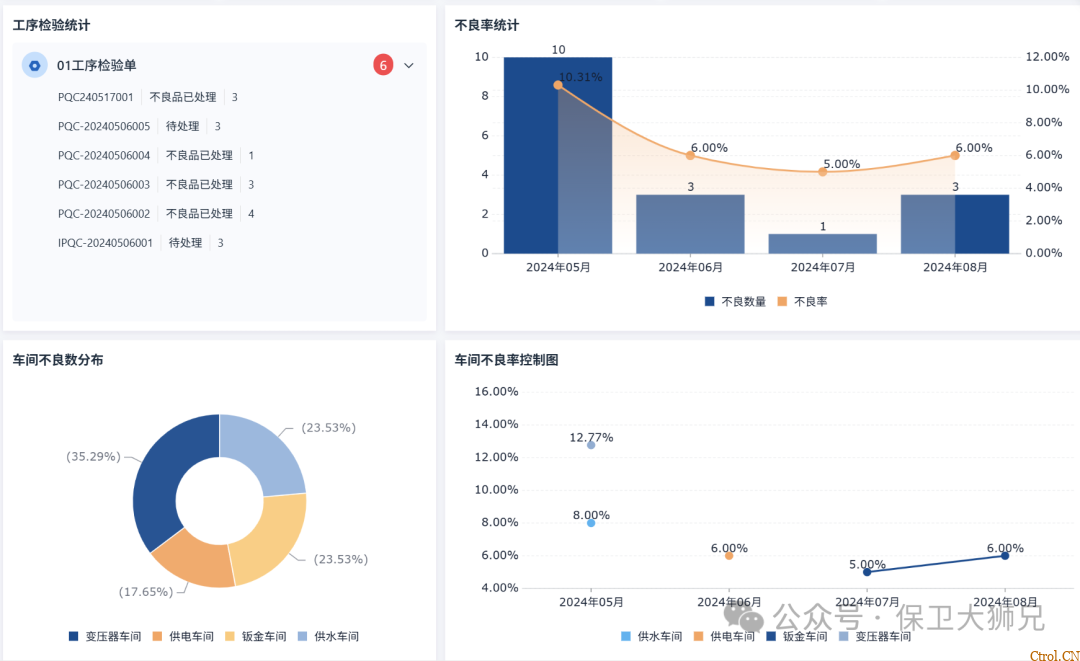
常见风险:
- 车间温湿度波动,影响产品成型或尺寸;
- 粉尘、静电控制不严,导致电子产品失效;
- 仓库、包装区环境不达标,成品运输途中出问题。
基础做法:
- 建立环境监控机制,关键岗位温湿度、洁净度实时监测;
- 制定5S、ESD防护等现场管理规范,定期检查整改;
- 特殊工序、特定季节,加严环境控制措施。
建议做法:
- 将环境监控数据、检验数据、异常记录打通,一旦环境超标,系统自动关联相关工序、产品、责任人;
- 所有环境巡检、5S检查、整改结果数字化存档,便于日常监督和客户审厂;
- 对环境变化敏感的产品,建议长期监控环境对质量的影响,提前预警。
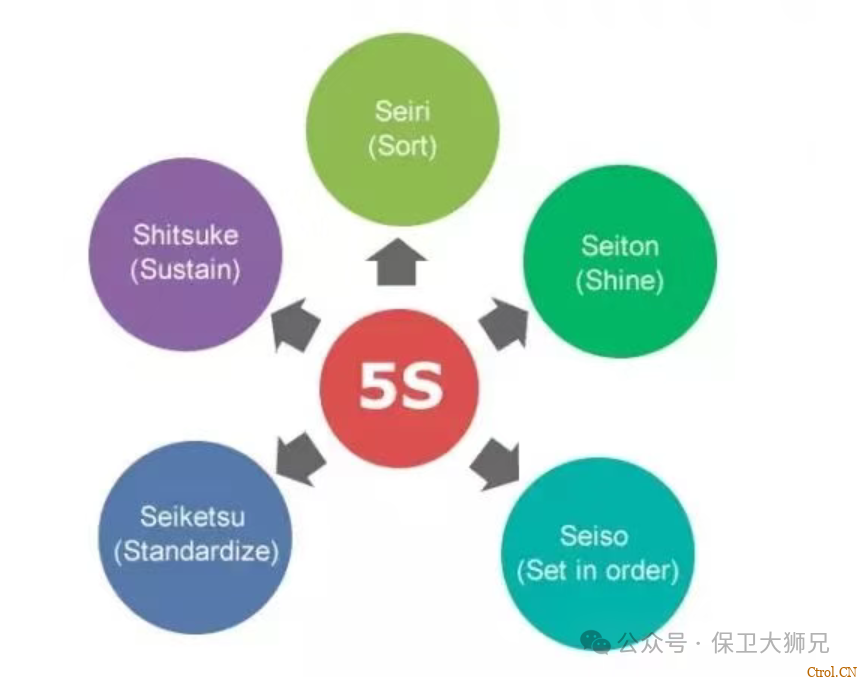
⑥ 测(Measurement)|测量不准,质量控制全白干
测量就是指生产过程中对各种数据、指标的测量和控制。产品是否符合质量标准,离不开严格的测量和检验。
如果测量环节出了问题,产品质量就会受到影响。
比如:
- 检验标准是否科学合理,能否真实反映产品质量?
- 检验工具是否准确,是否需要定期校准?
- 检验过程是否严格,是否存在漏检现象?
- 生产过程中的数据是否被实时监控?
建议做法:
很多企业在测量管理上,已经不止停留在“合格/不合格”,而是更进一步,做到:
- 不良品趋势、产线不良率,按月、按工序、按产品、按人员,全部自动统计;
- 不良品类型占比自动生成,哪个缺陷最多,一目了然;
- 每个员工的检验产量、报工质量、问题记录,全程透明;
- 在制品、生产计划、质检结果,全部挂钩到系统里,实时监控、动态预警。
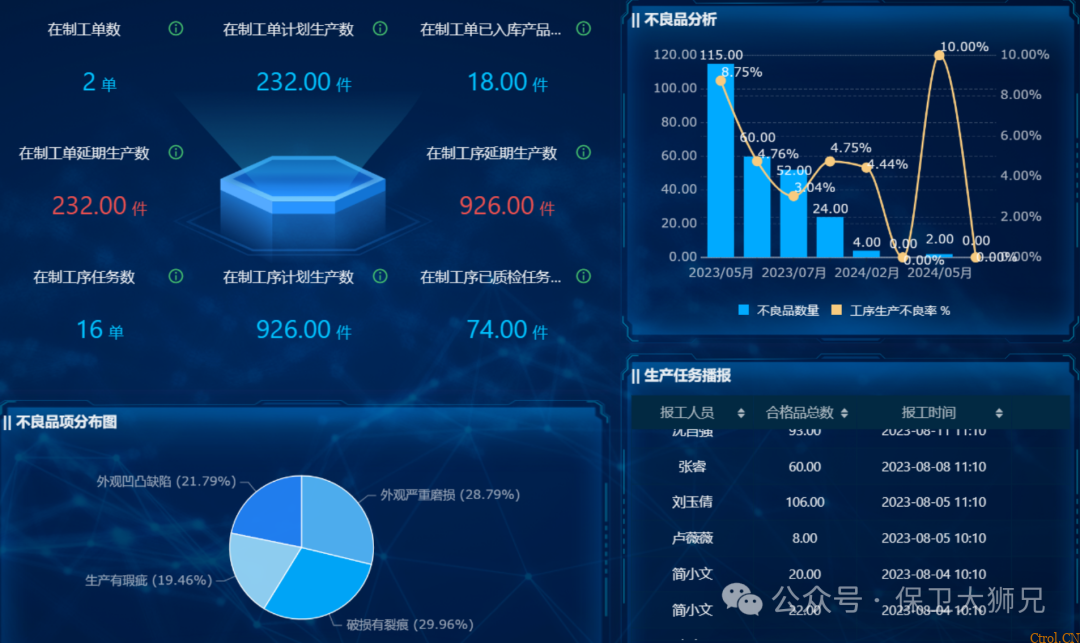
很多工厂的人在处理质量问题时,习惯性地“头痛医头、脚痛医脚”: 操作员出错,就抓培训;设备坏了,就修设备;材料批次不稳,就盯采购。
但实际上,绝大多数质量问题,根本不是单个环节出了问题, 而是多个环节叠加、多个因素联动的结果。
真正高效、靠谱的质量管理,必须从整体去看, 把“人、机、料、法、环、测”六大要素,作为一个整体来管理。
1. 绝大多数质量问题,都是多因素叠加出来的
在真实的生产现场,很多质量问题,表面看起来是单一环节的锅, 但一深挖,几乎全是多因素叠加:
- 材料有波动,设备也不稳定,工艺又不细致,最终产品尺寸超差;
- 操作员误操作,工艺文件不严谨,测量环节也有漏洞,导致不良品流出。
- 质量问题发生的背后,往往是人、机、料、法、环、测多要素“联合作案”。
如果还只盯单个环节去管,问题就会反复、改不彻底。
2. 六大要素之间,本质上是彼此关联、相互牵连的
这六个要素,从来都不是“单独存在”的,每一个环节都会影响其他环节:
- 人和法:操作员执行能力,往往和工艺标准是否清晰、易操作有关;
- 机和料:设备状态直接影响材料加工效果,设备带病运转,材料再好也白搭;
- 环和测:环境温湿度变化,直接干扰测量精度,导致数据误差放大。
换句话说,这六个字,不是一盘散沙,而是一张“网”: 任何一个点出问题,都会带动其它环节的波动。
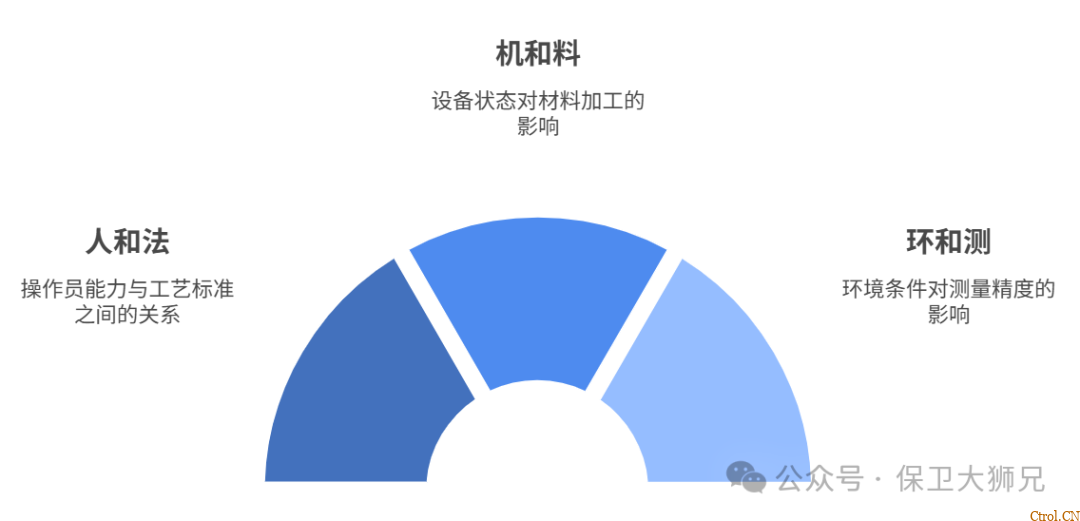
高水平的质量管理,最根本的原则,就是不单独看问题、必须整体联动管控。
实际操作中,最有效的方法,就是把六个要素和质检流程、问题闭环流程彻底联动起来:
- 来料检验(IQC) → 材料(料)+ 供应商管理;
- 工序检验(PQC) → 人、机、法、环、测全面交叉;
- 成品检验(FQC) → 工艺(法)+ 检验(测)的终点防线;
- 发/退货检验、库存检验 → 环境(环)、测量(测)、工艺(法)的后段保障;
- 样品管理、客户投诉、质量事故管理 → 直接反映全流程、全要素的运行质量。
质检流程跑得越细,六要素的协同越扎实,问题越少。
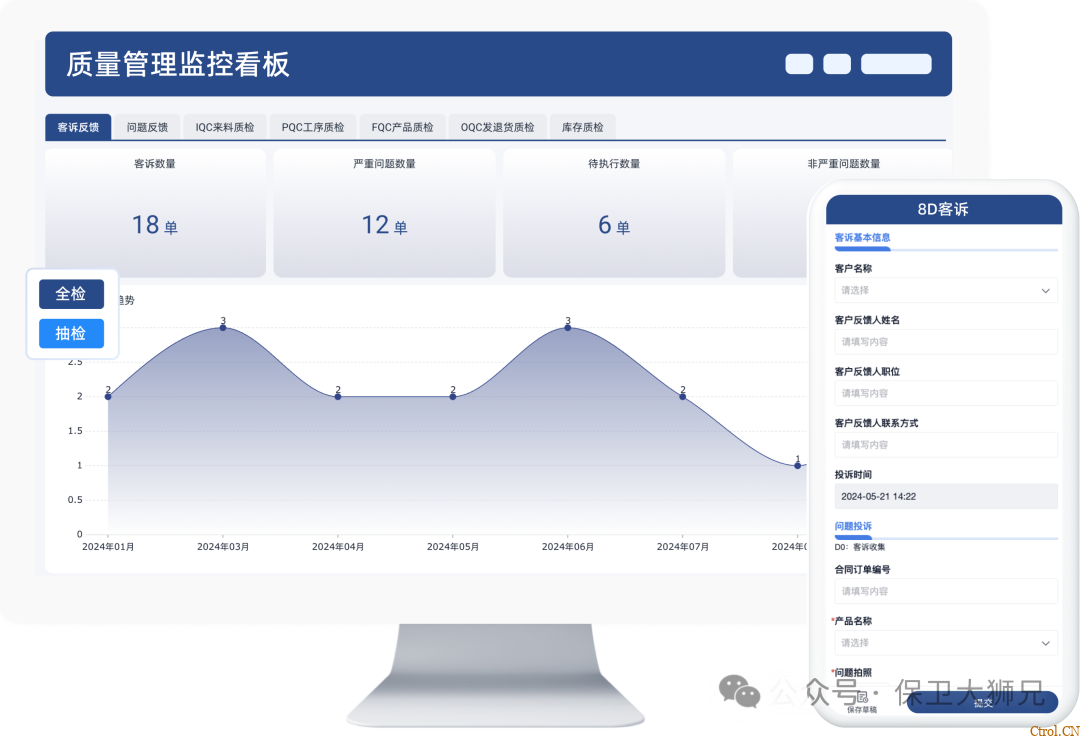
必须一口气带着六个字去查,“人、机、料、法、环、测”六个角度全覆盖;
同时,对照质检流程,把每一环节的检验、记录、责任、异常全部拉通检查。
- 查人、查机、查料、查工艺、查环境、查测量,六个要素全面对齐;
- 拉出全部质检记录、异常单据、整改单、审批记录,做完整的交叉比对;
- 彻底找清问题根因,整改、验证、归档,全链条留痕。
只有把问题当成“整体系统”去解决,才能避免反复出错。
4. 问题分析框架
这里推荐一套组合工具,把问题原因和对策措施一并梳理,效率很高:
先用特性要因图(鱼骨图),从六个要素“人、机、料、法、环、测”全面梳理问题根因;
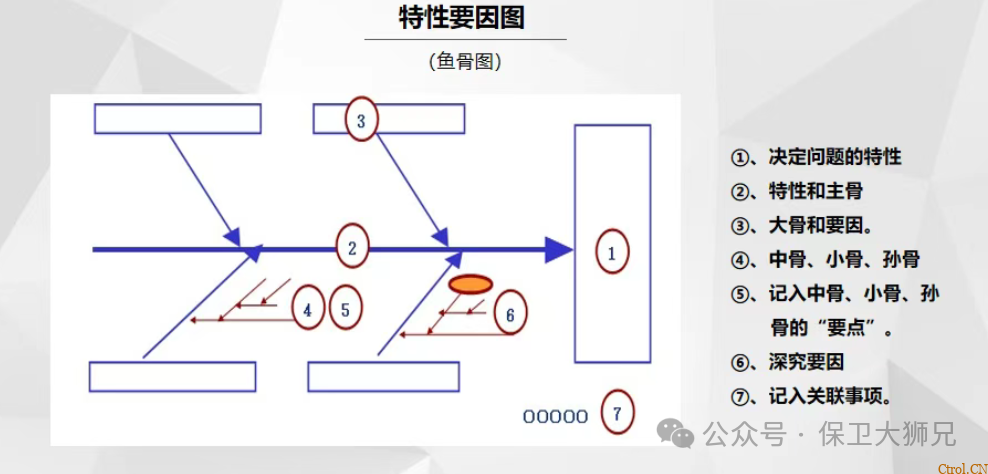
这套工具的核心优势,就是把“问题”和“对策”一图到底,所有责任人、措施、时间、效果一目了然,避免空谈对策。
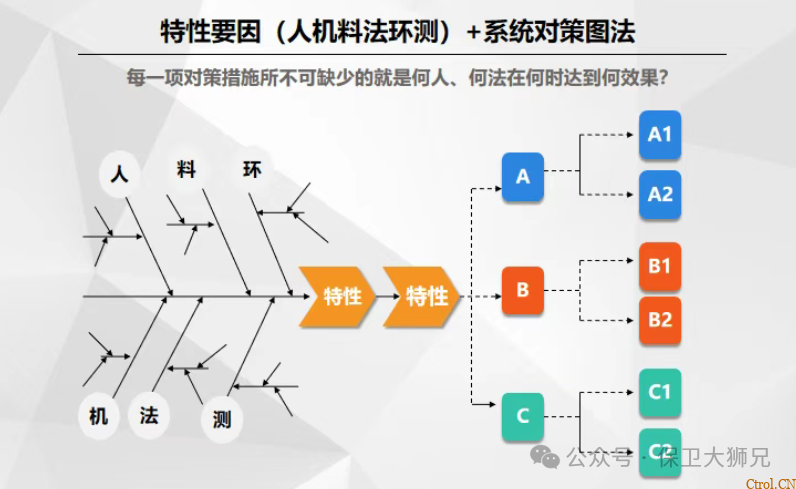
无论企业规模大小、产品种类复杂与否,人、机、料、法、环、测,始终是质量管理的基本盘。
这些年,很多工厂谈“数字化”“智能制造”, 但说到底,哪怕技术再先进,质量的根子还是在这六个字上。
只要工厂里有人在操作、有设备在运转、有物料在流动,这六个字就不会过时。
更重要的是,质量管理,从来都不是靠某一个环节“突击”, 真正有用的办法,始终是整体联动、协同管理、闭环管控:
- 把这六个字当成一个系统去盯;
- 把质检流程跑顺,让问题止步于流程之内;
- 把问题闭环机制跑通,做到有问题必查、有整改必落、有数据必留。